Personal Care Products Industry
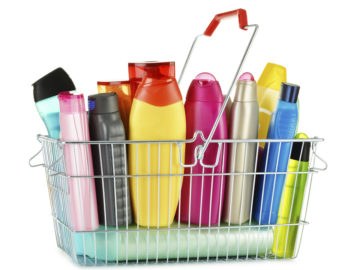
Our customers in the personal care and sanitation industry continually share with us the challenges they face and opportunities they see within their industry. Many of these companies are looking to increase production and to grow their business, both within the U.S. and globally. One of the emerging trends for Fortune 500 companies, in industries such as personal care, household cleaning, and disinfectants includes more integrated packaging machinery operations. Their goal is to upgrade conventional packaging equipment to more technologically advanced solutions that not only reduce changeover times and other human factors, in plants where thousands of SKUs and case sizes are involved, but also to track functions and tie operational monitoring back to a central hub.
Overview
Personal care and sanitation industries require manufacturers to monitor the quality of their products from source to shelf to prevent defect or damage returns while maintaining strict levels of sanitation. This means engineering and plant managers have an ever-increasing load of responsibilities. They manage a rapidly increasing number of product SKUs and the scheduling of multiple product runs on a single packaging line. They are called upon to review energy consumption, down time, changeovers and packaging waste. They are also expected to conserve valuable resources by finding ways to maximize production and operational effectiveness.
The Challenge
The burden of SKU proliferation is a commonly cited challenge in the personal care industry and its effects on production are often underestimated. SKU growth can have the following major plant impacts:
- Running out of plant space
- More labor is needed to get same amount of work done
- Reduced “capacity” or the inability to deliver the right product just in time and on time
- More frequent case size changeovers that diminish throughput
- Products and packaging being placed in storage configurations that create hazardous plant conditions
Implementing leading-edge packaging equipment into the production line can help maximize line flexibility for SKU expansion and ensure a quality product from design to shelf.
The Wexxar Bel Solution
The Wexxar Auto Adjust machines, such as the WF30 Fully Automatic Case Former and BEL 290 Fully Automatic Case Sealer, are built with standard features like pre-set box recipes and operations monitoring to help customers with these responsibilities. Paired together as a complete solution with case packing stations, this solution becomes the Flex E Pack, a solution that that can be easily upgraded at any time to suit your growing needs. Key performance benefits include:
- Safety - operators don’t have to access the inside of the machine and extra safety guarding is included
- Operation efficiency – faster set-up and changeover
- Increased productivity - reliable and repeatable changeover
- Enhanced operating experience – easy touch screen interface for quick operations monitoring
- Ease of changeover - automatic size changes using menu presets
The Wexxar Auto Adjust system also allow production managers to monitor the packaging systems at a single-source because these machines tie easily into existing line programming, for optimization, and analysis by the manager. Plant managers can specifically monitor the dynamics of their production lines, including tape levels and operational speed management. The Auto Adjust machine ensures that changeovers are reliable. Furthermore, box recipes allow operators to select from pre-set box sizes and start packaging new products with minimal dialing in and running in of test boxes.
The WF30 case former with Auto Adjust features a compact design for machinery of this class and fits easily into most packaging line applications. The machine offers touch-screen controls, Pin-and-Dome case opening system that ensures precise forming and bottom flap folding, fully-interlocking Safe Logic safety guarding, which protects operators when accessing the machine; tool-less case size changeover and extruded aluminum frame construction.
Application requirements can vary in different industries and the needs from one packaging operation to another may be as diverse as handling an oversize case, a fragile case, or conveying or accumulating on demand but the need for reliable and repeatable changeovers matched with monitoring and ease of use is universal.
The end result is Fortune 500 companies are using new technologies like the Auto Adjust to improve system performance, changeover reliability, and ROI, in the short term. They are moving to maximize line flexibility and monitoring for the future. Auto Adjust delivers a lower cost of ownership overall.